How Does a Cyclone Separator Work? A Simple Guide to Industrial Dust Collection
- Aida Ghani
- Nov 6, 2024
- 7 min read
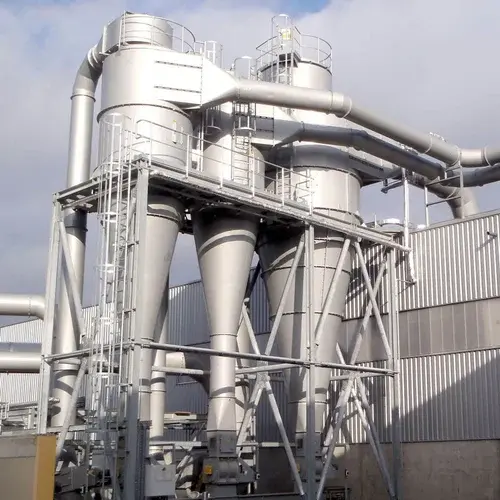
Tired of clogged filters, constant maintenance, and dust clouds hanging around your equipment? A cyclone separator might be the answer. Built for heavy-duty dust collection, a cyclone dust separator clears out particles by spinning them out of the airflow—no filters needed. That means cleaner air, less maintenance, and fewer interruptions on the job.
If you’re managing a plant or facility, understanding how a cyclone separator dust collector works can give you an edge. This guide will walk you through the basics, the benefits, and why a cyclone separator could be the right call for your industrial dust collection system.
What is a Cyclone Separator?

A cyclone separator is a straightforward piece of equipment with a tough job: separating dust and other particles from the air before they get into your machinery. It works by creating a controlled vortex, spinning incoming air at high speed. This forces heavier particles to the outer edge of the separator, where they settle out and can be collected, leaving cleaner air to exit through the top.
In industrial settings, especially where dust and debris are part of daily operations, cyclone dust separators make life easier.
They’re commonly used in industries like wood processing, cement, and metalworking—anywhere dust buildup can wreak havoc on equipment or reduce air quality. Unlike standard filters that need frequent changing, cyclone separators don’t clog easily, making them a reliable choice for dust-heavy environments.
By relying on centrifugal force instead of filters, cyclone separators keep maintenance low and efficiency high. If your operation generates a lot of dust, a cyclone separator dust collector could be the solution that keeps your air clean and your equipment running smoothly.
Breaking Down The Key Components of a Cyclone Separator
A cyclone separator might seem simple, but it’s designed with precision to handle tough, dust-filled environments. Let’s break down the main parts that make it work:
Inlet: This is where the dust-laden air enters the cyclone. The inlet’s design directs the airflow in a way that sets up the spinning motion needed to separate out particles.
Cylindrical Body: Once inside, the air spins rapidly along the cylindrical section. This spinning motion is key—it creates the centrifugal force that pushes heavier dust particles outward, separating them from the air.
Conical Section: Below the cylinder, the cone narrows, forcing the spinning air to compress. This compression increases the speed and efficiency of particle separation, sending heavier particles straight down to the collection area.
Outlet: The cleaned air, now free of most dust and particles, exits through the top of the cyclone separator. This outlet is typically designed to release air back into the environment or direct it through another filter if needed.
Dust Collection Chamber: At the base of the cyclone, separated dust
particles fall into a collection chamber. This is where dust is gathered and can be disposed of without any impact on airflow or efficiency.
Each part of the cyclone dust separator plays a specific role in keeping dust out of your equipment. With this setup, cyclone separators handle high dust loads without filters that clog, giving you a reliable, low-maintenance option for keeping the air clean and the machinery clear.
How Does a Cyclone Separator Work?
At first glance, a cyclone separator might look like a simple cone, but it’s built to harness some serious physics. Here’s how it works, step by step:
Air and Dust Enter: Dust-laden air is pulled into the separator through the inlet, where it’s directed into a spiraling motion. This spinning action is essential for separating the dust from the air.
The Cyclone Effect: Inside the cylindrical section, the air spins rapidly, creating a vortex. Think of it like a mini-tornado inside the separator. This vortex generates centrifugal force, which pushes heavier dust particles toward the outer walls.
Particle Separation: As the particles hit the walls, they lose momentum and begin to slide downward. The cone shape of the separator helps force these particles toward the bottom, where they can be collected.
Clean Air Exits: Once the dust is separated, the cleaned air rises through the center of the vortex and exits through the outlet at the top. The design ensures only cleaner air leaves the separator.
Dust Collection: Meanwhile, the dust particles fall into the collection chamber at the base. With no filters to clog up, the system keeps running smoothly, handling large amounts of dust without the need for frequent maintenance.
This spinning, dust-separating action is what makes a cyclone separator dust collector so effective. By relying on centrifugal force, it keeps dust where it belongs—in the collection bin—while letting your equipment breathe easy.
Benefits of Using Cyclone Separators in Industrial Settings
A cyclone separator isn’t just about keeping the air clean—it’s about keeping your operation efficient and your equipment protected. Here are some key benefits of using a cyclone dust separator in heavy-duty environments:
Low Maintenance: Unlike traditional filters that clog and need frequent replacements, a cyclone separator uses centrifugal force to do the heavy lifting. No filters mean fewer stoppages, fewer maintenance checks, and lower costs over time.
Efficient Dust Collection: Cyclone separators handle high dust loads with ease, capturing particles before they reach sensitive equipment. For industries like metalworking, wood processing, and cement production, keeping dust out of machinery is a game-changer for minimizing downtime and extending equipment life.
Improved Air Quality: With a cyclone separator dust collector, cleaner air is released back into the workspace, making for a safer environment. This is a big win in operations where dust clouds can affect both worker health and visibility on the floor.
Cost-Effective Solution: Investing in a cyclone separator means a long-term solution with minimal upkeep. Lower maintenance needs and increased equipment longevity directly impact the bottom line, making it a smart choice for budget-conscious operations.
How to Keep Your Cyclone Separator in Top Shape
A cyclone separator is designed to be low-maintenance, but keeping it running at peak performance does require a few routine checks. Here’s how to make sure your cyclone dust separator keeps doing its job without a hitch:
Regular Inspections: Check the cyclone body and the dust collection chamber periodically. Look for any signs of wear or build-up that could affect performance. Over time, some components might need tightening or minor adjustments to keep the airflow optimal.
Clear the Dust Collection Chamber: Emptying the collection chamber regularly keeps the separator running smoothly. If the chamber gets too full, it can impact airflow and reduce separation efficiency. Set a regular schedule based on your dust levels to keep it clear. In addition, installing sensors to monitor dust loading and plugging may be able to preemptively alert your team before a clog or backup occurs.
Inspect for Air Leaks: Cyclone separators rely on strong airflow. Any leaks in the system can compromise its efficiency. During routine maintenance, check all connections, seals, and any joints where air might escape. Tightening these can make a noticeable difference in performance.
Monitor the Inlet and Outlet: Dust buildup in the inlet or outlet can cause clogs over time, especially in heavy dust environments. Monitor or clean these areas occasionally to maintain proper airflow and ensure your industrial dust collector performs efficiently.
Check Alignment and Fastenings: Ensure that the separator and all its parts are correctly aligned and securely fastened. Misalignment or loose parts can reduce efficiency and lead to premature wear, impacting both performance and safety.
A few quick checks here and there can go a long way toward maximizing the lifespan and effectiveness of your equipment.
Dust Control in Action: How Industries Rely on Cyclone Separators
In the industrial world, an industrial dust collector like the cyclone separator dust collector is essential in environments where dust is a constant issue. Here are a few scenarios where cyclone separators and industrial dust collection systems make a significant impact:
Wood Processing Plants: In woodworking, sawdust and wood particles are everywhere. Without effective dust collection, these particles can clog equipment, impact air quality, and create safety hazards. Many wood processing plants use cyclone dust separators as part of their industrial dust collection systems to manage large volumes of sawdust, keeping machinery clear and the workspace safer.
Metalworking Facilities: Grinding, cutting, and welding produce significant amounts of fine metal dust. A cyclone separator captures these particles before they reach other equipment, preventing damage and reducing wear and tear on ventilation systems. This keeps metalworking facilities running smoothly and extends the lifespan of their industrial dust collector setups.
Cement Manufacturing: Cement production generates fine particles that can be difficult to manage with traditional filters. By using a cyclone separator, cement plants handle high dust volumes efficiently, keeping the air clear and reducing the risk of dust buildup in production areas. In these facilities, a reliable industrial dust collector supports both air quality and equipment reliability.
Grain Processing: In grain handling and processing facilities, dust from grain particles isn’t just a nuisance; it’s a safety hazard. Cyclone separators are used here to keep dust levels down, helping industrial dust collection systems in these facilities reduce the risk of combustible dust accumulation and maintain clean processing areas.
Each of these industries benefits from an industrial dust collector like a cyclone separator, which can handle large dust volumes with minimal maintenance.
Choosing the Right Solution for Industrial Dust Collection
When it comes to dust control, a cyclone separator offers a simple, reliable solution to keeping your workspace clean and your equipment running smoothly. By separating out dust without the hassle of filters, cyclone dust separators minimize downtime and maintenance costs—key advantages for any industrial operation.
At Midwest Custom Engineering, we understand the demands of heavy-duty environments, and our industrial dust collection systems are built with durability and efficiency in mind.
Our cyclone separators are designed to handle high dust loads with ease, providing a dependable choice for industries that can’t afford interruptions. If you’re considering a dust collection upgrade, MCE’s cyclone solutions are ready to meet the challenge.
Reliable dust control starts with the right equipment.
Explore our cyclone separators that keep the air clear and the downtime low.
Comments